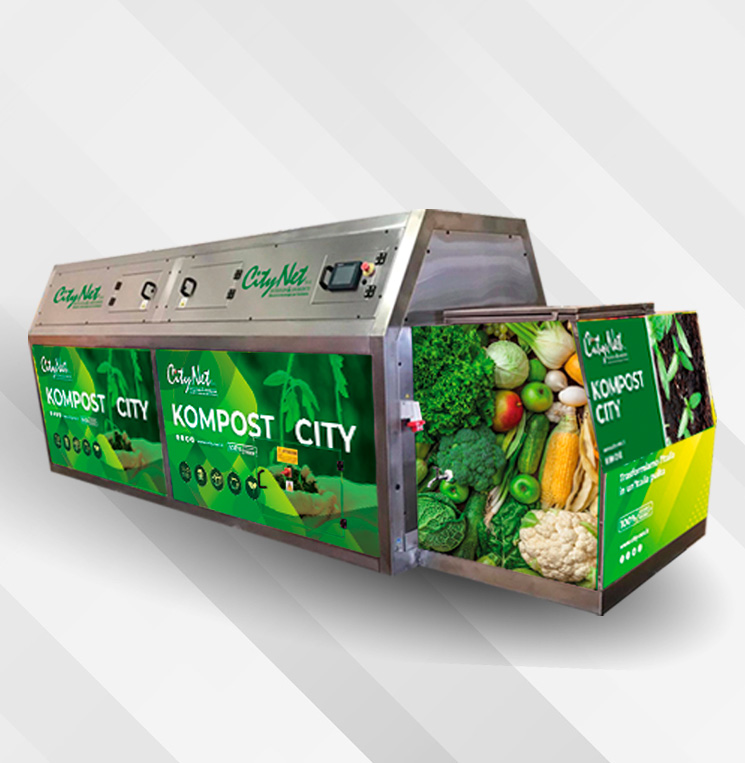
Electromechanical composter with aerobic cycle model KCE
The Aerobic Cycle Electromechanical Composters model KCE is a SINGLE CHAMBER with ROTATING CYLINDER with the ability to modulate according to the required days, the management of the continuous flow of the entire composting process from the loading phase of the organic waste to the automatic COMPOST unloading phase.
All composters model KCE are made with a supporting structure in hot galvanized FE 42 steel and the remaining parts (cylindrical composting chamber, liquid-tight heads, external canopies, pipes and biofilter) in AISI 304 stainless steel.
Exclusive Benefits
COMPLETE ABSENCE OF INPUT SHREDDING
The decision not to shred the incoming organic matrix stems from the fact that the same produced at home and not, contains a percentage of foreign fraction, which today is estimated on average in the order of 5-10%.
If this foreign fraction is crushed together with the organic matrix, it actually causes its pollution and is difficult to separate from it.
IN ADDITION, the non-shredding of the organic matrix allows a better oxygenation and then one better oxidation of the composting material, avoiding the formation of areas with high compaction that can cause triggers of anaerobic process and therefore the production of gas and bad smells inside the composting chamber.
COMPLETE ABSENCE OF MOVING ORGANS IN THE COMPOSTING CHAMBER
The choice to use the technology of the single rotating cylinder chamber is the result of a project of great technical simplification, since in the absence of mechanical moving parts inside the composting chamber, it is they avoid machine stops due to blocking of the internal mechanical parts, caused by accidental breakage or by the bags that wrap around them until they are blocked, thus having to empty the machine to replace the damaged mechanical parts.
MANAGEMENT OF THE COMPOSTING PROCESS
Temperature stabilization through a automated system of automatic hot air sufflation, inside the rotating cylinder of the composting chamber.
SIMPLICITY OF USE AND GREAT REDUCTION CAPACITY
The KCE model composters are born from a project that aims to create a machine capable of transforming the domestic and non-domestic organic matrix into excellent compost, through a absolutely biological aerobic process, in an extremely simple way to use and manage.
This has meant that all composters model KCE models are fully automated, requiring no operator intervention other than the loading of the organic fraction and the structuring agent.
Thanks to their high-efficiency biological process, the KCE model composters have a reduction capacity of the compound organic fraction that averages 80%.
GOOD FOR THE ENVIRONMENT
Transforming waste into resources is the rationale behind responsible consumption.
Traditional separate collection organic waste, based on landfilling, has a considerable environmental impact. The decomposition of biodegradable organic waste in fact produces methane (greenhouse gas) and generates substances capable of contaminating the soil and groundwater. Landfills also generate bioaerosols, odors and visual disturbances and are high transport costs. They also occupy a large amount of space, representing an irrecoverable loss of resources and land, resulting in a negative impact on the environment and biodiversity.
About 3% of Australia's total greenhouse gas emissions come from organic matter that rots anaerobically (without air) in landfills. To consider this data in a comparable context, it roughly corresponds to the emissions produced by the aeronautical sector of the whole country.
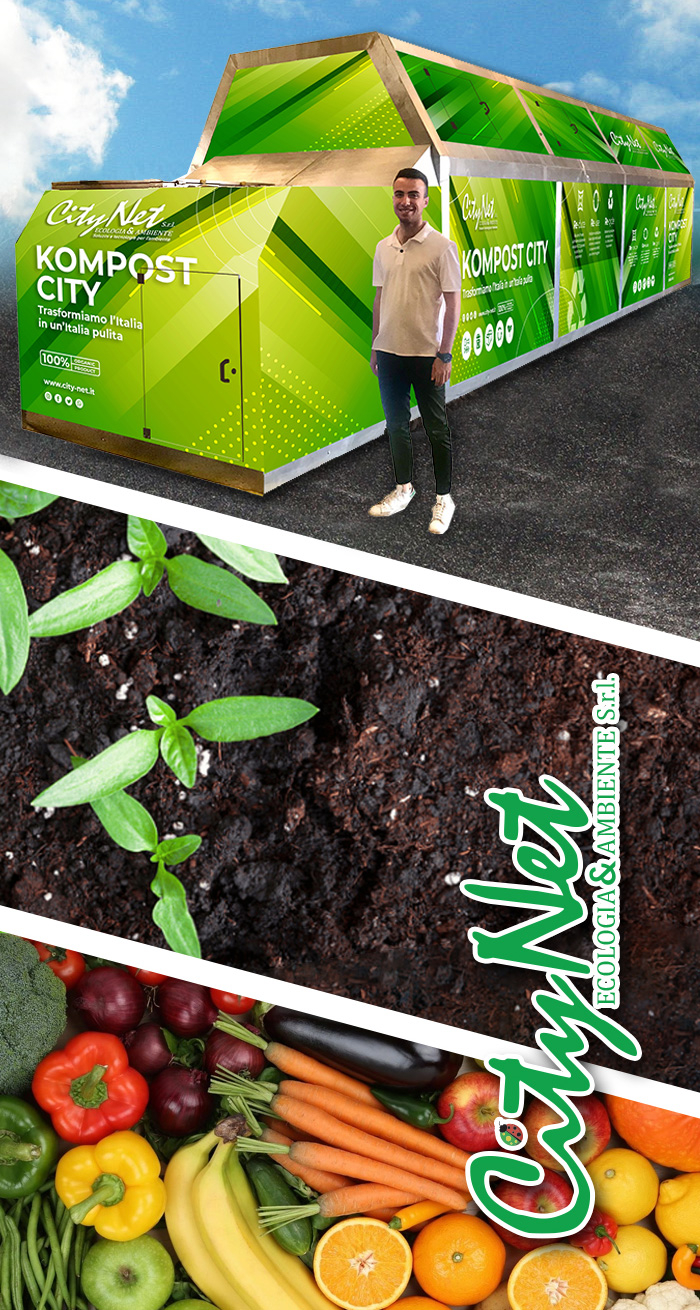
80%
Reduction of the volume of waste conferred, in 35 days
93%
CO2 equivalent savings
100%
Fertile soil returned
Environmental advantage
The use of electromechanical composters with aerobic cycle model KCE considerably reduces the amount of waste that ends up in landfills, the cause of CO2 emissions, leachate, pollution of groundwater and soil, in addition to the impact on the environment caused by transport.
Practical advantage
Electromechanical composters with aerobic cycle model KCE have a design that adapts to the environment in which they will have to operate, they are odorless and efficient, they optimize the processes and return a fertile and nutritious soil that can be reused.
Economic tax advantage
The Aerobic Cycle Electromechanical Composters KCE model give the possibility to access, in Italy,
to the following concessions:
50% refund for tax credit (Industry 4.0)
10% relief thanks to the "Nuova Sabatini"
Reduction up to 30% on the waste tax
for domestic and industrial composting
SUBSTANTIVE DIFFERENCES BETWEEN SINGLE CHAMBER AND ROTATING CYLINDER COMPOSTERS AND SINGLE CHAMBER OR MULTI CHAMBER COMPOSTERS WITH INTERNAL HANDLING ORGANS.
DESCRIPTION | WE | COMPETITION | DIFFERENCES / ADVANTAGES |
Types of process |
Areobic | Areobic | Nobody |
Type of room | Unique rotating without internal mechanical parts | Multi-camera with internal arms | The single chamber with rotating cylinder allows a feeding and a continuous cycle process. This is because in the first phase of the process, a thermophilic phase is generated which remains permanently active and easily guarantees the achievement of a temperature of at least 55 ° C which is the minimum required by law to guarantee the "Sterilization" of the organic material being treated.
The slow gradual and continuous movement of the material, by means of the rotation of the composting chamber, ensures that the thermophilic phase always remains active and that the material delivered daily enters a phase that is already thermally active. This aspect is very important for what concerns the guarantee of the perfect sterilization of the treated material at a sanitary level. Composers with multi-chambers, with two or more chambers, must necessarily have a discontinuous process flow, in fact, once the first chamber is loaded, one must wait for the material inside it to activate the thermophilic process phase and exceed the time required by the legislation, then wait the times to reach at least a temperature of 55 ° C and then allow the material to remain at this temperature for at least 72 hours. Only after this phase can the material be mechanically moved from the first chamber to the next one where it will undergo the mesoflla phase. These machines periodically require (approximately every 15 days) routine maintenance which involves opening the doors of the machine to free the internal arms from any mater B envelopes that wrap around the axis of the arms, slowing down their movement until they are blocked. This activity, to be carried out with the machine loaded, does not comply with the health and hygiene safety regulations as inside the chambers there is waste in an active process with decomposition and therefore vapors and odors induced by the process itself. |
Type of advancement | Continuous | Discotinuno | In our single chamber system with rotating cylinder, the advancement of the material takes place continuously and automatically as the waste just conferred (heavier) pushes forward the lighter one that has passed the first Thermophilic phase to be transferred to the subsequent Mesophilic phase. , and then exit automatically. All the above process, automatically stabilized in temperatures, reduces the weight of the organic fraction conferred on average by 80%.
After a certain number of days in the multi-chamber, the waste remains in the first chamber, where it carries out its thermophilic process, then mechanically must be transferred to the second chamber to then exit not automatically but by manual emptying. In this type of machine the waste is moved and then made to advance with arms supported by a shaft which, by rotating, move the waste and make it move forward. The shaft and the arms inside the composting chambers can potentially be subject to mechanical breakages which can create downtime for their replacement and / or repair. Furthermore, the movement from the first to the second chamber actually creates the zeroing conditions of the thermophilic process, forcing the restart of the process from its initial phase at each load. This dynamic means that on many occasions the biological process with the initiation of the thermophilic phase has longer times and difficulty in reaching the temperature that guarantees its sterilization which we remember for lesge must be at least 55 ° C to be maintained for at least 72 hours. . |
Level of load of the rooms |
75%-80% | 50%-55% | In our single chamber, the total absence of any mechanical organ inside, together with the loading point positioned in the upper part of the chamber, allow the chamber to be loaded to the 75-80% of its volumetric capacity.
In multi-chamber composters, equipped with internal shaft and arms for handling, the loading can hardly exceed the 50%-55% in order not to tire the handling arms beyond the breaking point. |
Automatic heating Inside the room of composting |
Here I'm | ? | The heating system inside the composting chamber guarantees the sterilization of the composting material, guaranteeing the hygienic and sanitary aspect. |
SUBSTANTIVE DIFFERENCES BETWEEN SINGLE CHAMBER AND ROTATING CYLINDER COMPOSTERS AND SINGLE CHAMBER OR MULTI CHAMBER COMPOSTERS WITH INTERNAL HANDLING ORGANS.
DESCRIPTION | WE | COMPETITION | DIFFERENCES / ADVANTAGES |
Process type | Areobic | Areobic | Nobody |
Type of room | Unique rotating without internal mechanical parts | Multi-camera with internal arms | The single chamber with rotating cylinder allows a feeding and a continuous cycle process. This is because in the first phase of the process, a thermophilic phase is generated which remains permanently active and easily guarantees the achievement of a temperature of at least 55 ° C which is the minimum required by law to guarantee the "Sterilization" of the organic material being treated. The slow gradual and continuous movement of the material, by means of the rotation of the composting chamber, ensures that the thermophilic phase always remains active and that the material delivered daily enters a phase that is already thermally active.This aspect is very important for what concerns the guarantee of the perfect sterilization of the treated material at a sanitary level. Composers with multi-chambers, with two or more chambers, must necessarily have a discontinuous process flow, in fact, once the first chamber is loaded, one must wait for the material inside it to activate the thermophilic process phase and exceed the time required by the legislation, then wait the times to reach at least a temperature of 55 ° C and then allow the material to remain at this temperature for at least 72 hours. Only after this phase can the material be mechanically moved from the first chamber to the next one where it will undergo the mesoflla phase. These machines periodically require (approximately every 15 days) routine maintenance which involves opening the doors of the machine to free the internal arms from any mater B envelopes that wrap around the axis of the arms, slowing down their movement until they are blocked. This activity, to be carried out with the machine loaded, does not comply with the regulations of health and hygiene safety as inside the chambers there is waste in an active process with decomposition and therefore vapors and odors induced by the process itself. |
Type of advancement | Continuous | Discotinuno | In our single chamber system with rotating cylinder, the advancement of the material takes place continuously and automatically as the waste just conferred (heavier) pushes forward the lighter one that has passed the first Thermophilic phase to be transferred to the subsequent Mesophilic phase. , and then exit automatically. All the above process, automatically stabilized in temperatures, reduces the weight of the organic fraction conferred on average by 80%. After a certain number of days in the multi-chamber, the waste remains in the first chamber, where it carries out its thermophilic process, then mechanically must be transferred to the second chamber to then exit not automatically but by manual emptying. In this type of machine the waste is moved and then made to advance with arms supported by a shaft which, by rotating, move the waste and make it move forward. The shaft and the arms inside the composting chambers can potentially be subject to mechanical breakages which can create downtime for their replacement and / or repair. Furthermore, the movement from the first to the second chamber actually creates the zeroing conditions of the thermophilic process, forcing the restart of the process from its initial phase at each load. This dynamic means that on many occasions the biological process with the initiation of the thermophilic phase has longer times and difficulty in reaching the temperature that guarantees its sterilization which we remember for lesge must be at least 55 ° C to be maintained for at least 72 hours. . |
Load level of the rooms |
75%-80% | 50%-55% | In our single chamber, the total absence of any mechanical organ inside, together with the loading point positioned in the upper part of the chamber, allow the chamber to be loaded to the 75-80% of its volumetric capacity. In multi-chamber composters, equipped with internal shaft and arms for handling, the loading can hardly exceed the 50%-55% in order not to tire the handling arms beyond the breaking point. |
Automatic Heating Inside the composting chamber | Here I'm | ? | The heating system inside the composting chamber guarantees the sterilization of the composting material, guaranteeing the hygienic and sanitary aspect. |